Boost operational efficiency and reduce downtime with on-site, 24/7 access to essential items.
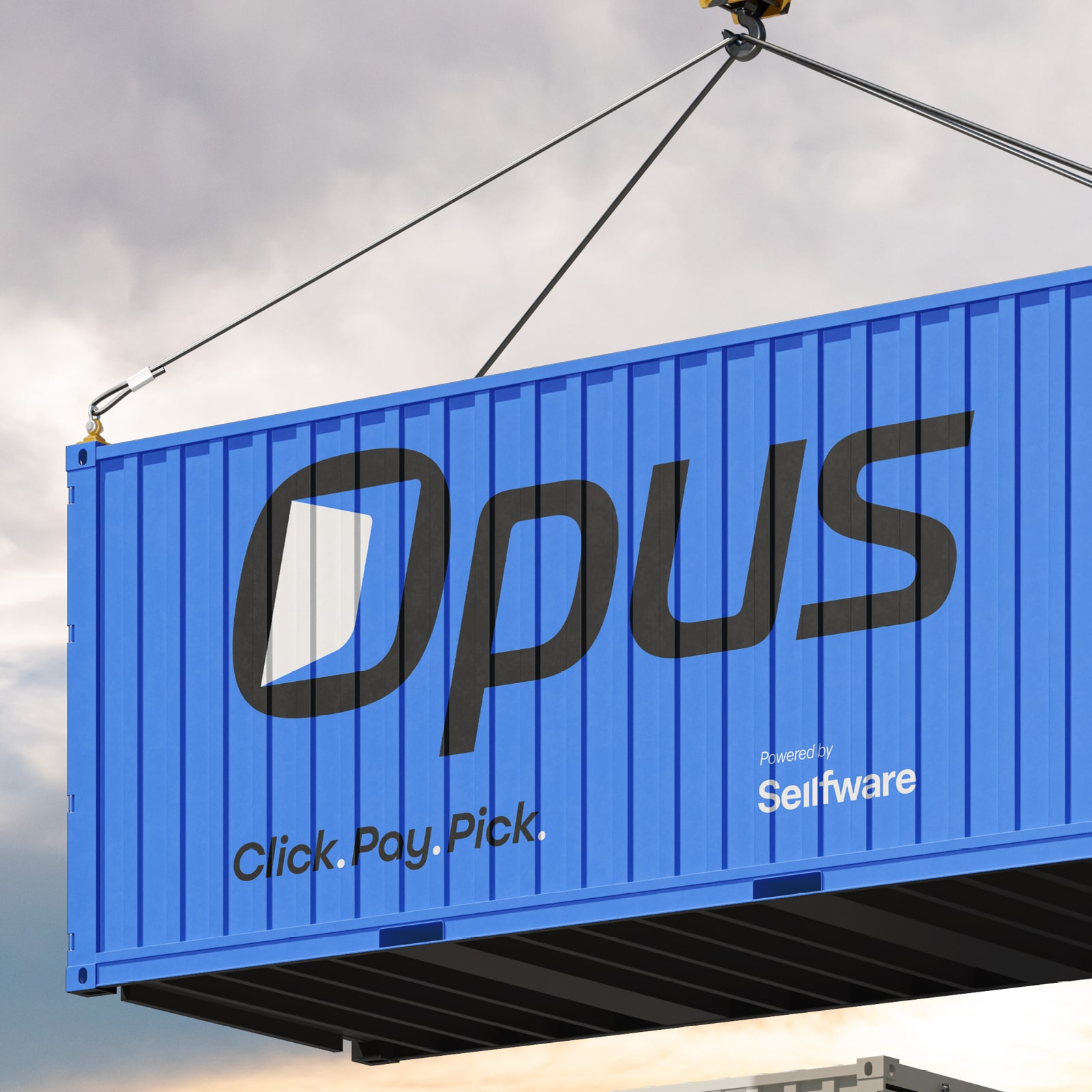
Problems we solve
Tighter supply chains mean that any unplanned delay in the supply of materials can impact the flow of production. Not holding enough stock to hand at the right time impacts output and increases cost from just-in-time deliveries.
An increased reliance on automation places more importance on the supply of spare parts, which aren't always held locally for maintenance and repair, causing orders to be missed if machinery technology cannot be fixed quickly.
Whilst some plants may have the space to hold stock, keeping a controlled supply of the spare parts in the right place is a challenge. Buying stock adds costs and does not help unless 100% accurate.
Reduce downtime with access to critical items when you need them
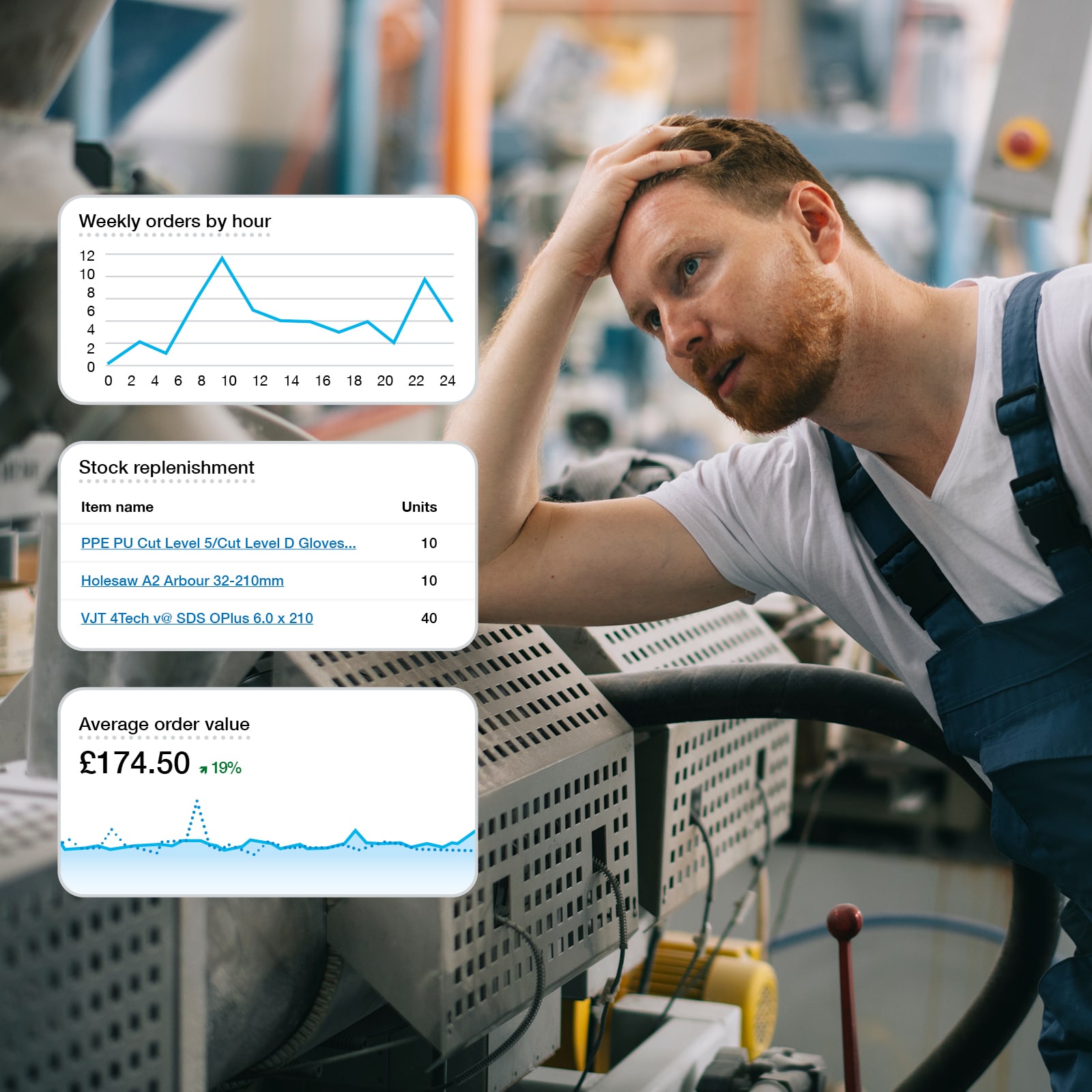
Remove unwanted costs with visibility of stock levels and in demand items
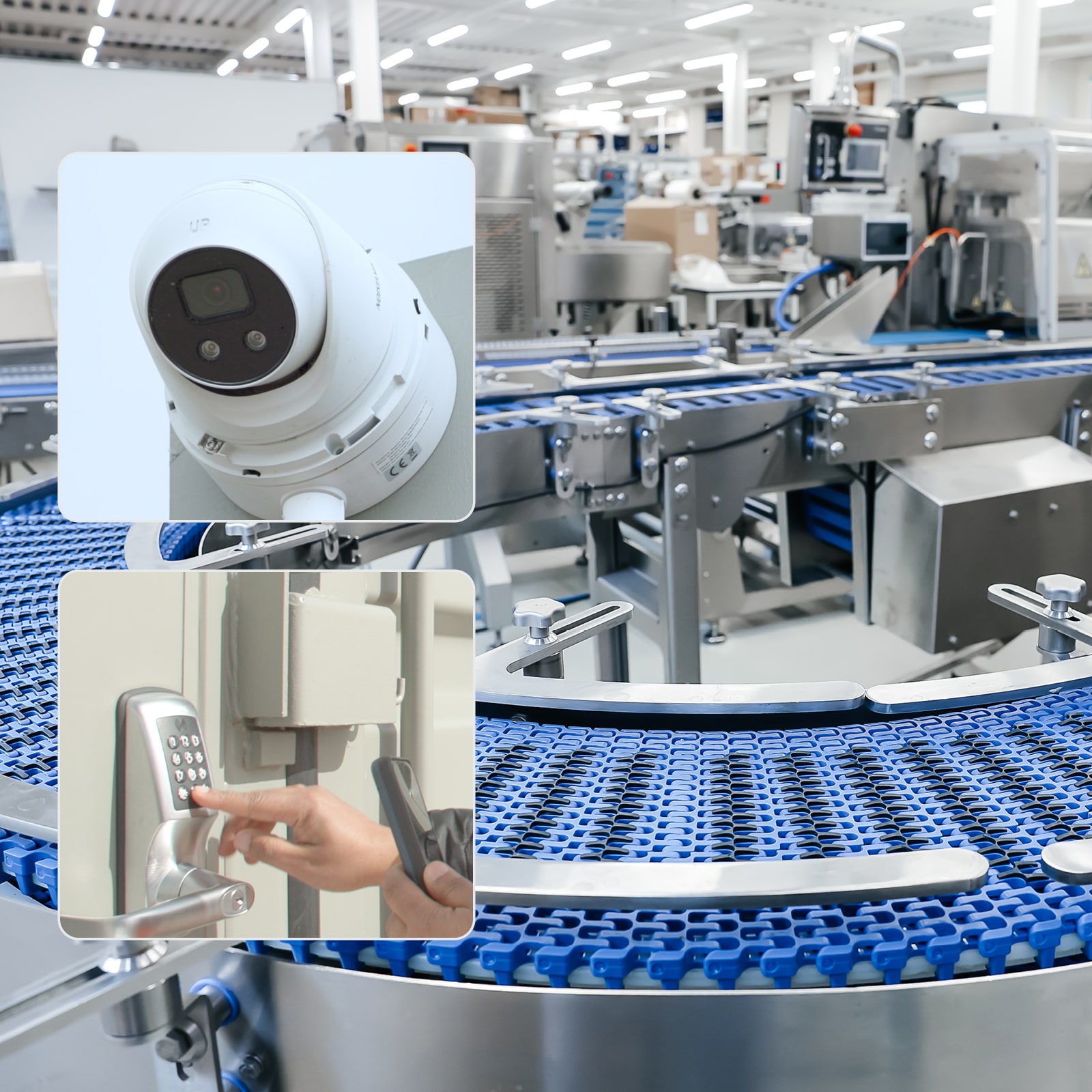
Improve your carbon footprint with fewer deliveries to facilities
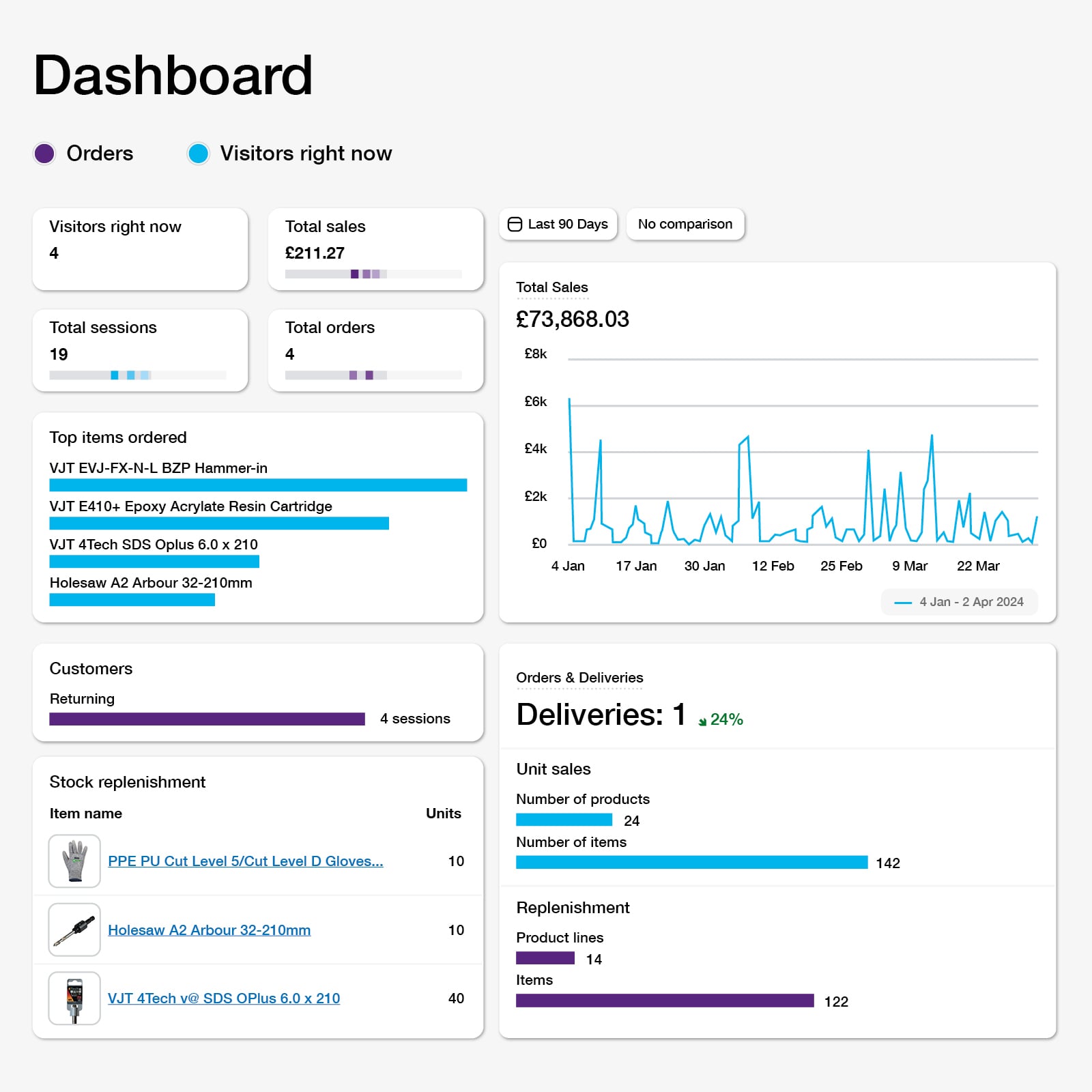
Speak to our team
If you are a leading manufacturer and would like to learn more about Opus, speak to our client success team, who will be happy to discuss implementation and capabilities.